By Marshall L. Henley
I thought I would share my V2.0 plane with everyone. I can honestly say it's the second CombatONE I've built since the V1.0 prototype, but I've built ten wings in the mean time. I've been tweaking that process to get to something that we can speed build pretty fast (airframe at least - radio installation takes time as usual).
First, I'll share some pics and comments, then I'll explain V1 vs. V2. Both will fly great, and both should be easy to build. If you attended the first build instruction at the Club Meeting three months ago (May meeting), then you can build a V1 and compete with a V2 no-problem. However, V2 has some advantages and builds a little faster. It is possible that it will be a couple of ounces lighter.
Just in case you're not sure where to look, click here for the CombatONE page our our website. The plans for V2 and the ribs (V3.1) are there.
PICTURES OF MY V2.0 BUILD
Since I was not able to make it to the field tonight due to work obligations, I stayed up and put the finishing touches on the V2 and shot these pics.

Geoff Biderman had used an aileron doubler for his. I liked the idea for two reasons:
- It lets you set the control horns deeper in the aileron for more glue "bite."
- Along with 1, assuming the same control horn heighth as a less deep cut, this means you'll get more throw from the same size horn. I'm getting 45 degrees up and down, so I have more than enough throw.
Geoff had made his doublers full-span. I wanted to keep a thin trailing edge, so I made mine thick where the "bending moment" was highest - where the servo was applying torque, then I tapered it off down the aileron.
You can also see the V2.0 trailing edge of the wing in front of the aileron - something different than in V1. The top and bottom skins come all the way back. We used to cut the spar from the trailing edge of the bottom skin, but with the rib that made the wing asymmetric.
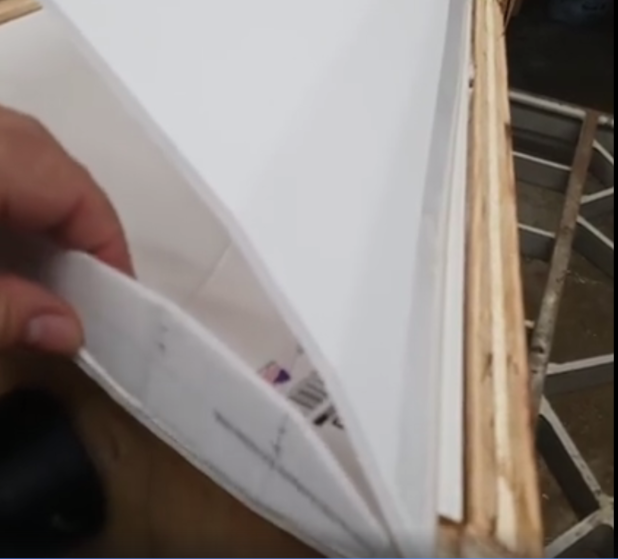
V2 uses a simple double-crease for the wing and a rib and spar to form the airfoil. That and keeping the top and bottom skins the same are about all the truly substantial changes from V1 to V2.
I used simple ink-jet white copy paper graphics on my V2. Keep the top of the wing white, and you can do some pretty cool stuff by just printing, snipping out and spraying with 3M Super 77 contact cement spray. You don't even have to cut it very clean; the white-on-white makes the lines pretty much disappear. Other than that, you can see that V2 is the same footprint as V1.

Look closely at the bottom of this pic and you'll see that mine weighed in at just under 27 ounces. That's including the bigger 3536/9 motor and a 3300mAh high voltage lipo battery from Revolectrix. The battery is the most expensive thing in this picture!

Here's an up-close of the battery installation. Jim Beerman had used a plywood sheet beneath his battery with a strap glued under it. I think it was a suggestion from Bob Scheppele. It was a good one. However, I think the foam board in a double layer with the bottom layer cut out partially for the strap will work. The glue holds the strap, which is in turn glued to the battery mount, which is velcroed (underneath) to the battery. Of course, where there's no strap there's a double-layer of foam board sandwiched with hot glue, so I'm betting this never comes out. Either way (plywood or foamboard), we're getting too crazy with these things during combat to just use sandwiched velcro between the battery and the wing: we need a strap.

You probably noticed my "pod" in the last couple of photos. Here's another shot. I just wanted something to stuff the battery wires into. Totally unnecessary, but for what it's worth, it only took a few minutes and it worked out well.

To make things easier, I "pre-mounted" the servo on these platforms. I cut the hole beneath the servo extra large by about 1/16" all around, and this allowed me to adjust the servo while the glue was hot so I didn't have to use subtrim. Well, almost. Somehow, something changed after I started messing with endpoints, so I ended up using some subtrim anyway on one side. The idea is sound. I'm thinking I'll have to test for endpoint adjustments before I commit to gluing it in for the final "no subtrim" position.

You might have noticed that I beveled most of everything in this plane. Not necessary, however, we do have to bevel the leading edges of the wing skins and the leading edge of the ailerons, and I'm building a lot of these, so...
I built the above tool to make beveling easy. I found out the hard way that you don't want to absent mindedly grab for a tool sitting next to this one though.
V1 vs V2 table
The following table details the main difference between the V1 and V2 design (not necessarily things I did differently between the V1 and V2 prototypes, like graphics on the wing):
V1
|
V2
|
3 wing creases
|
2 wing creases
|
Wing creases cut and glued to hold shape
|
Wing creases just creased, no glue, no cutting
|
No rib
|
Rib at root to form airfoil
|
Bottom wing skin shorter than top
|
Wing skins identical
|
Spar cut from bottom wing skin
|
Spar cut from section on left of left-most wing in the cut sheet view of the plans
|
Single thickness ailerons
|
Optional: I doubled the thickness of the ailerons at the front and full-span at the center-most area of the ailerons. This is completely unnecessary, but it is helpful for rigidity.
|
Let me know if you have any questions. Thanks!
--Marshall